射出成形の不良対策|発生原因、トラブルシューティング、品質改善方法を解説
射出成形プロセスにおいて、不良品の発生は避けられない問題です。これらの不良は製品品質に直接影響を与えるだけでなく、生産コストの増加や納期の遅延をも引き起こす可能性があります。そのため、射出成形における不良対策は、製造業において非常に重要な課題となっています。
本記事では、射出成形で発生する代表的な不良の種類とその原因、短期的なトラブルシューティング方法、そして長期的な品質改善戦略について詳しく解説します。さらに、最新技術であるガスインジェクションとカウンタープレッシャー技術を活用した不良対策についても触れ、より効果的な品質管理方法を提案します。
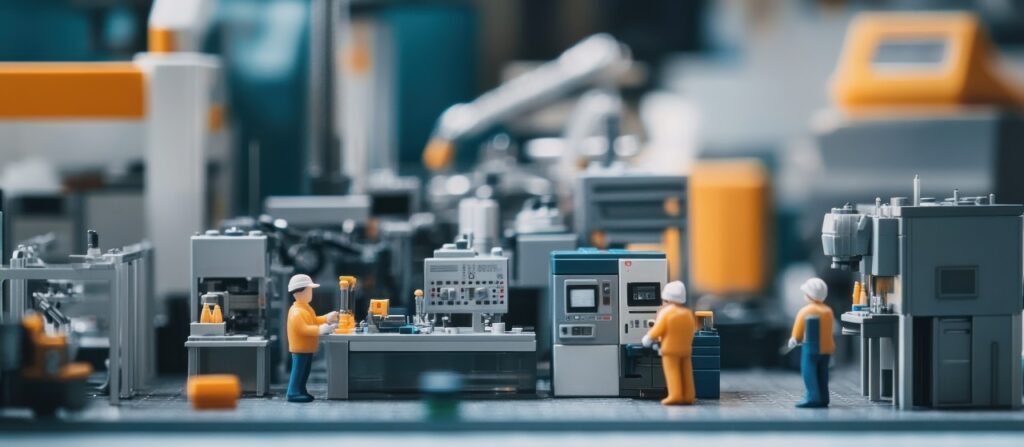
射出成形における代表的な不良の種類と発生原因
射出成形プロセスでは、様々な種類の不良が発生する可能性があります。代表的な不良として、ヒケ(シンクマーク)、バリ、ウェルドライン、ショートショットなどが挙げられます。
ヒケ(シンクマーク)は、成形品表面に現れる凹みや窪みのことを指します。これは主に樹脂の収縮が不均一な場合や、冷却速度が不適切な場合、また射出圧力や保圧が不足している場合に発生します。
バリは、成形品の分割線や端部に発生する余分な樹脂のことです。金型のクリアランスが大きすぎる場合や、射出圧力が高すぎる場合、あるいは樹脂温度が高すぎる場合に発生しやすくなります。
ウェルドラインは、成形品表面に現れる線状の痕跡を指します。これは複数の樹脂流動が合流する際に発生し、樹脂温度や金型温度が低すぎる場合に特に顕著になります。
ショートショットは、成形品の一部が充填されずに欠けている状態を指します。射出速度や圧力が不足している場合、樹脂温度が低すぎる場合、あるいは金型温度が低すぎる場合に発生しやすくなります。
短期的な不良対策:すぐに実施できるトラブルシューティング
各不良に対して、短期的な対策を実施することができます。例えば、ヒケ対策としては、射出圧力を上げることで樹脂の充填を改善したり、冷却時間を延長して均一な収縮を促進したり、金型温度を適切に調整して冷却速度を制御したりすることが効果的です。
バリ対策では、射出圧力を低減して過剰な圧力によるバリの発生を抑制したり、適切な温度範囲内に樹脂温度を設定したり、金型のクリアランスを確認し必要に応じて調整したりすることが有効です。
ウェルドライン対策としては、樹脂温度を上昇させて流動性を向上させ合流部の接着を改善したり、金型温度を上昇させて樹脂の冷却速度を遅くし合流部の接着を促進したり、ゲート位置を最適化して樹脂の流れを改善しウェルドラインの発生を最小限に抑えたりすることができます。
ショートショット対策では、射出速度と圧力を増加させて樹脂の充填を促進したり、樹脂温度を上昇させて流動性を向上させたり、金型温度を上昇させて樹脂の流動性を維持し充填を促進したりすることが効果的です。
長期的な不良発生予防と品質改善のための戦略
長期的な品質改善のためには、プロセス全体の見直しが重要です。生産効率と不良発生率の関連性を分析し、最適な生産条件を確立することが求められます。また、定期的なメンテナンススケジュールの策定と実施、設備の更新計画の立案と実行も重要な要素となります。
さらに、品質管理システムの導入も効果的です。統計的プロセス管理(SPC)を導入することで、データに基づいた品質管理を実現することができます。また、IoTを活用したリアルタイム監視システムを導入することで、センサーによる成形パラメータの常時モニタリングや異常の早期検出、自動アラートシステムの構築が可能となります。さらに、AIを活用した予知保全を実施することで、過去のデータを分析し、不良発生を予測することもできます。
ガスインジェクションとカウンタープレッシャー技術を活用した不良対策
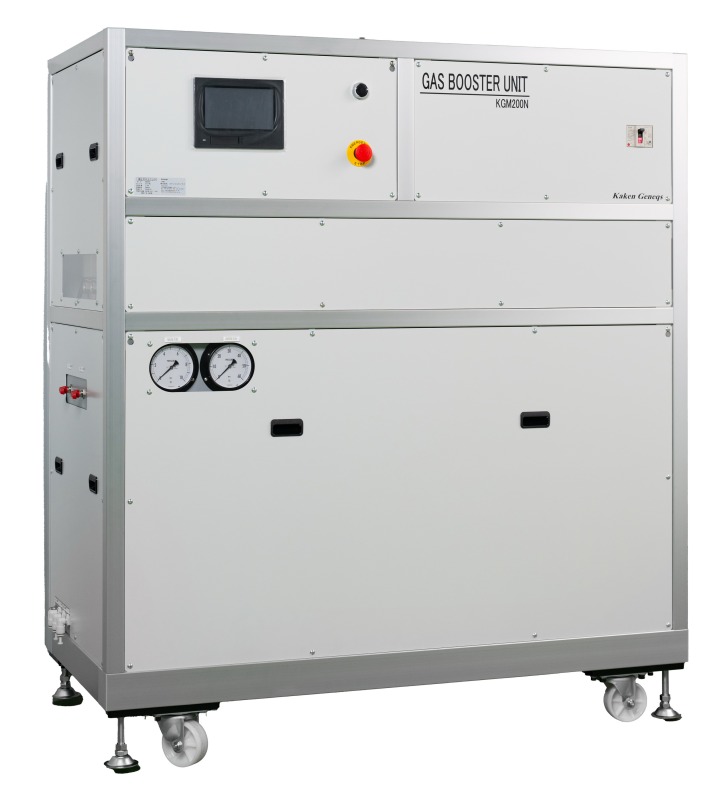
ガスインジェクション技術
最新技術を活用することで、より効果的な不良対策が可能となります。ガスインジェクション技術は、成形中に不活性ガスを射出して中空構造を形成する技術です。
これにより、製品の軽量化と形状精度の向上が実現できます。不良対策としては、ヒケやソリの改善に効果があります。
カウンタープレッシャー技術
カウンタープレッシャー技術は、発泡成形時に金型内を事前に圧縮ガスで加圧し、発泡樹脂を射出した後に一気に圧力を放出することで、スワールマークを抑えます。これにより、ソリッド成形同様に美しい表面仕上げを保ちながら軽量化が実現できます。
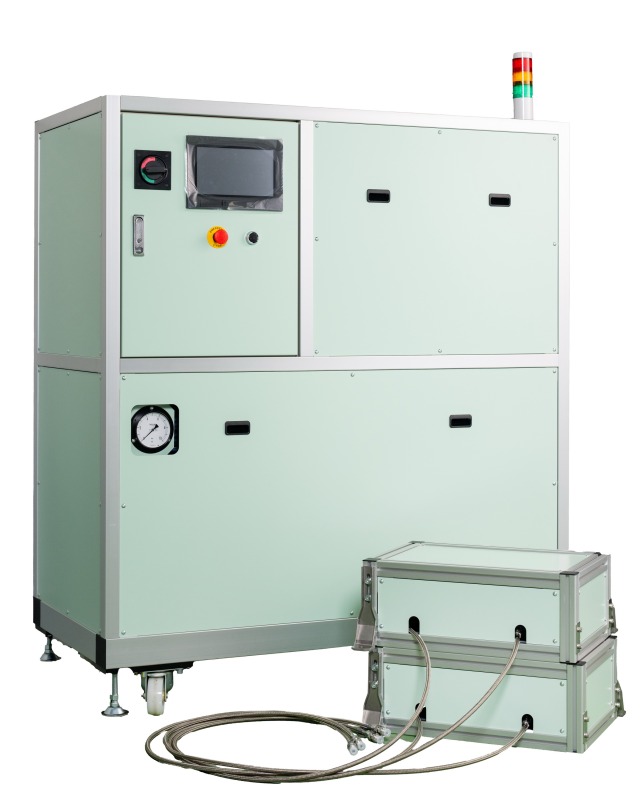
これらの最新技術を適切に活用することで、従来の方法では対応が困難だった不良にも効果的に対処することが可能となります。ただし、これらの技術の導入には初期投資や技術習得が必要となるため、長期的な視点での検討が重要です。
以上の対策を総合的に実施することで、射出成形プロセスにおける不良発生を大幅に削減し、製品品質の向上と生産効率の改善を達成することができます。継続的な改善活動と最新技術の導入を通じて、競争力のある製造プロセスを構築していくことが重要です。